Probentransport in der industriellen Qualitätssicherung am Beispiel der Granulierung
Die konstante Prozessüberwachung ist Grundpfeiler der modernen Qualitätssicherung. Nur durch regelmäßige Überwachung kann sichergestellt werden, dass das produzierte Material den Anforderungen entspricht. Dabei ist es unerheblich, ob es sich um einen Prozess in der Lebensmittelindustrie, der Medizin oder der Chemie handelt. Kernelement der Prozessüberwachung ist der Regelkreis bestehend aus den Schritten
- „Aufnahme von Prozessparametern“,
- „Analyse von Parametern“,
- „Ableiten von Anpassungsanforderungen“ und
- „Durchführen der Änderungen“
ähnlich dem PDCA-Zyklus oder auch Deming-Zyklus.
Die, zur Steigerung der Produktion, immer schneller ablaufenden Produktionsabläufe bedürfen auch eine immer enger getaktete Überwachung. Dies hat zur Folge, dass die Zeit, die zum Beispiel in der Lebensmittelbranche zwischen Probenahme und dem Erhalten von Messdaten liegt und die früher Stunden gedauert hat, immer kürzer werden muss.
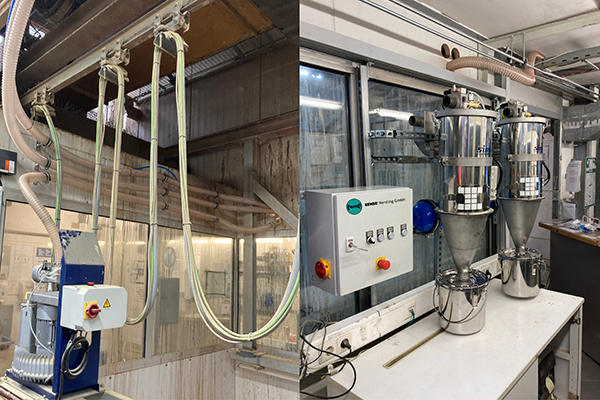
Granulat
Unter Granulierung wird im Allgemeinen der Prozess verstanden, bei dem ein oder mehrere Pulver in eine körnige Form, die sogenannten Granalien gebracht wird. Dies kann entweder über Druck oder mit Hilfe eines Bindemittels geschehen. Es gibt verschiedene Gründe für eine Granulierung, wie z.B.
- Vermeidung von Entmischung des Materials aufgrund unterschiedlicher Partikelgrößen
- Durch eine geringere Adhäsion des Granulats gegenüber dem Pulver erhöht sich die Fließfähigkeit
- Das Granulat besitzt ein geringeres statisches Aufladungspotential, als das Pulver
- Durch die größeren Partikel wird die Staubkontamination herabgesetzt
Wie jeder andere Prozess, muss auch die Granulierung überwacht werden. Dazu eignen sich Probenehmer, die auf möglichst produktschonende Art eine Probe entnehmen, wie z.B. Tassenprobenehmer.
Diese Probenehmer werden in Prozessen eingesetzt, in denen es auf eine maximale Produktschonung ankommt. Dadurch, dass das Material in einer Probentasse gesammelt wird, kommt es zu keiner Beeinträchtigung des Materials, wie zum Beispiel, wenn das Material mit einer Schnecke entnommen werden würde. Nach der Probenahme folgt der Schritt der Probenanalyse, zum Beispiel mit einem Partikelanalyser oder einem Nahinfrarotspektrometer, um mögliche Abweichungen vom Soll-Zustand und somit mögliche Anpassungsanforderungen abzuleiten.
In diesem Zusammenhang ist es relevant, an welcher Stelle im Prozess die Probenahme und die Analyse stattfindet. Hierbei werden die vier Konzepte „Inline“, „Online“, „Atline“ und „Offline“ unterschieden. Die untenstehende Grafik veranschaulicht diese Zusammenhänge.
Ziel muss es sein, die Probenahme möglichst nah am Prozess durchzuführen, genauso wie die Analyse. In vielen Unternehmen ist es aktuell noch der Fall, dass die Proben zwar direkt aus dem Prozess entnommen werden und repräsentativ und reproduzierbar sind. Jedoch ist es häufig so, dass die Analyse an anderer Stelle, in einem anderen Gebäude oder sogar bei einem externen Dienstleister durchgeführt werden.
Durch den Transport des Materials vom Ort der Probenahme zum Ort der Analyse, kann es bereits zu Veränderungen der Materialparameter kommen, das heißt, dass sich das Material in der Analyse anders darstellt, als es sich innerhalb des Prozesses verhält. Ein weiterer, deutlich kritischer Aspekt ist jedoch, dass es zwischen Materialentnahme und -analyse zu erheblichen zeitlichen Differenzen kommen kann. Unter Berücksichtigung des eingangs beschriebenen Regelkreises führt dies zu einem erheblichen Performanceverlust, da sich die Laufzeit des Regelkreises um mehrere Stunden, bis hin zu Tagen verzögert.
Pneumatischer Probentransport
Seit Ende 2022 gehört das Unternehmen „SIMAR® GmbH“ fest zur REMBE® Alliance. Damit wurde die Gruppe, zu der bereits Unternehmen wie die „REMBE® Safety + Control GmbH“ und die „REMBE Kersting GmbH“ gehören um einen sehr wichtigen Partner erweitert. Ein Teil des Kerngeschäfts von SIMAR® ist der pneumatische Transport von Schüttgütern. Hierbei gilt es viele Punkt zu beachten, um die Qualität der entnommenen Materialien nicht zu beeinflussen und um ein unverfälschtes Analyseergebnis zu erzielen.
- Produktschonung: das Material darf in seinen Eigenschaften während des Transports nicht beeinflusst werden. Zum Beispiel muss die Kornzermahlung und die Materialentmischung auf ein Minimum reduziert werden.
- Stabilität: die einsetzten Rohre und Schläuche dürfen nicht abgerieben werden. Dies ist vor allem bei abrasiven Materialien ein wichtiger Aspekt
- Fremdmaterial: Es muss sichergestellt werden, dass es zu keinem Eintrag von Fremdmaterialien kommt
- Reinigung: Die Transporteinrichtung muss einfach trocken zu reinigen sein, damit es bei Produktwechseln zu keiner Verschleppung und damit zu einer Kreuzkontamination kommt. Dies ist vor allem bei der Verarbeitung von Stoffen mit hohen Anforderungen, wie FDA, Containment oder Toxizität relevant
- Kleinstmengen: Die Systeme müssen in der Lage sein auch Kleinstmengen von wenigen Gramm zuverlässig zu übertragen
Simar-Fördergerät
Für diese und ähnliche Anwendungsfälle hat Simar® ein Fördergerät entwickelt. Hierbei handelt es sich um ein Kompaktfördergerät extra für kleine Anlagen.
Das Fördergerät ist aus Edelstahl gefertigt und damit leicht zu reinigen und zu warten. Dadurch, dass es betriebsfertig geliefert wird, ist es einfach in bestehende Anlagen zu integrieren. Die Mikroprozessorsteuerung erlaubt eine Integration in das Leitsystem der Anlage. Das Fördergerät ist für Korngrößen von 0,5 – 5 mm geeignet. Die geringe Bauhöhe von nur 590 mm und der Verbrauch von nur 1,0 kW macht es zu einer guten Alternative zu großen Förderanlagen und damit ideal zur Nachrüstung in Zusammenhang mit der Installierung einer Probenahme.
Die Abbildung 3 zeigt den Aufbau und Funktionsweise des Kompaktfördergeräts. Über den Anschluss (1) wird der Vakuum-Kompressor angeschlossen, um ein Unterdruck zu erzeugen. An Position (2) wird das Material-Luft-Gemisch angesaugt und im Inneren des Behälters aufgefangen. Element (3) enthält die kompakte integrierte Steuerung. Nach dem Sammeln des Materials, kann das Fördergerät dieses über eine integrierte Klappe an weitere angeschlossene Systeme, wie zum Beispiel eine Flaschenabfüllung übergeben.
Geschwindigkeitszuwachs und Kostenersparnis durch Probentransport
Aufgrund der immer schneller ablaufenden Produktionsprozesse, ist heutzutage ein konstante Prozessüberwachung wichtig, um sicherzustellen, dass alle Anforderungen erfüllt werden. Das hat zur Folge, dass die Zeit zwischen Probeentnahme und -analyse kürzer werden muss. REMBE® Kersting möchte mit seinen Probenehmern sowie den passenden Fördergeräten einen Beitrag leisten die Entnahme und Analyse der Proben möglichst Inline, das heißt vor Ort, durchzuführen. Nur so kann konsequent und kurzfristig reagiert werden, falls die Materialparameter vom gewünschten Zustand abweichen. Am Ende ist es eine Frage der Kosten, die entstehen, wenn Material aufgrund von Fehlern verworfen werden muss.
Autor: Jonathan Blum, Dipl.-Wirt.-Ing. (Global Sales)